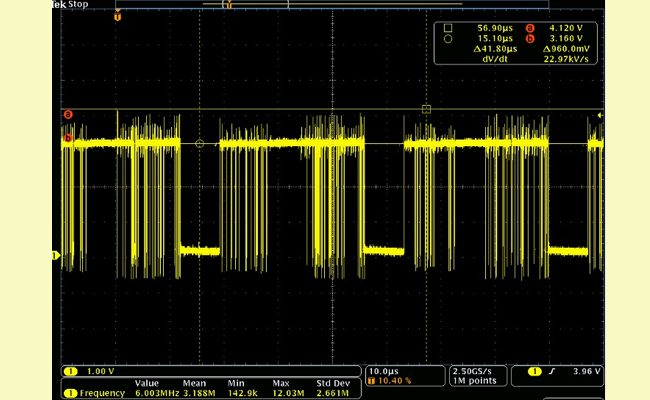
地面弹跳如何毁了你的一天
电源和接地反弹是集成电路(IC)上的电源和接地轨道相对于它们在PCB平面上的各自水平的位移。注入电源和接地路径的任何噪声都可能出现在逻辑输入和输出处。边缘率是最重要的,这可能会导致EMI问题。由于CMOS技术和模具收缩的进步,现代电子器件的开关边缘率远高于以前的技术。在这些类型的集成电路中,固有电特性的影响变得更加明显。
这些固有的电气特性之一是在所有引线框架材料中发现的电感,它产生电源或接地反弹。因此,减少地面反弹的设计策略在当今高速嵌入式和数字系统中起着不可或缺的作用。本文研究了液晶显示器组件产生的地弹,同时评估了地弹对系统级EMI的影响。分析了三种缓解地面弹跳的解决策略,并给出了每种策略的优缺点以及测试结果。
地面弹跳背景
通常所说的电源和地反弹实际上是I/O回路电感之间的电感耦合串扰。这种电感耦合串扰是在集成电路的宽数据总线共用一个公共的供、回引线时产生的,该引线具有如图1所示的寄生电感。同时开关噪声(SSN)通常被称为Vcc反弹或地反弹[3]。
图1:电源和地引线电感[4]
当信号回路从逻辑0切换到逻辑1时,充电所需的电流必须从功率子系统的电容中提取。此电流必须通过IC封装的Vcc引线的寄生电感。封装电感防止电流在这些快速边缘转换过程中流动。该电压瞬态驱动IC负极的电源(Vcc)轨道相对于PCB上的电源轨道,并在直流电源轨道[1]上产生振铃。
同样,当逻辑线从逻辑1切换到逻辑0时,传输线的寄生电容必须通过IC封装接地引线的寄生电感放电。这个di/dt作为一个强迫函数,在共有的返回寄生电感上产生电压降。该电压瞬态驱动IC正接地相对于PCB上的接地,并在接地面[1]上创建振铃。
电源和地轨中的这些不需要的瞬态是由单端逻辑驱动器对模上寄生电容器进行充放电造成的。安静输出将以与电源或地面反弹相同的波形移动。这些电压瞬变可以出现在离开IC的所有逻辑信号上。因此,它可以出现在离开IC的Vcc导轨、时钟线或数据线上。如果信号线有过多的供应或接地反弹,也可能导致逻辑故障。这些逻辑故障可以由制造商在产品原型阶段检测到。此单元产生的EMI问题在设备级上可能不严重,但在系统级上可能很严重。如果逻辑信号在没有屏蔽的情况下退出法拉第笼,则会引起电磁干扰[1]。将飞机上的多个点连接到“底盘地面”会使这些电流在底盘中流动,将其变成一个辐射面,从而恶化电磁干扰。这些问题与时钟无关。换句话说,低速PCB设计现在必须处理高速开关问题。
这个问题
作为我们下一代自主清洁机器人开发工作的一部分,我们开始做EMC预合规工作。我们的系统出现了多个电磁干扰问题。对EMI问题的进一步故障排除使我们将问题缩小到机器人平台中使用的触摸屏液晶显示器。
整个系统在一个EMC室中测试,远场天线保持在距离系统3米的地方。在这种情况下,图2所示的噪声来自安装了LCD的整个机器人系统的EMI扫描。
图2: 3米EMI测量前水平-机器人系统与液晶显示器Rev A
然后对机器人系统中使用的液晶显示器进行了单独测试,在一个带有远场天线的3米EMC室中使用外部电源供电。由24v外部电源供电时液晶显示器的EMI测量如图3所示。在将24v电源连接到LCD显示器进行额外的EMI测量之前,已验证24v电源没有EMI噪声。如图3所示,系统中有大量的电磁干扰,从~200 MHz到1 GHz(后来证实是由LCD显示器的地面和电源反弹造成的)。然后发现,当这个LCD单元连接到有多个pcba的系统时,LCD产生的噪声传导到各种电缆上,然后辐射到整个系统。
图3: 3米电磁干扰测量-前水平-液晶显示版本只有A
LCD显示组件由LCD显示单元和驱动器PCBA组成。液晶驱动器PCBA使用STM32F429IIT微控制器和176引脚LQFP封装。驱动程序PCBA使用24位RGB总线来连接LCD显示器。进一步的调查还显示,LCD驱动程序PCBA仅在微控制器上使用这种RGB数据总线提供了少数返回路径。LCD驱动器PCB堆叠分析显示通过PCB的电源层和接地层的痕迹。为了找到电磁干扰和液晶显示器上的问题来源之间的相关性,进一步调查了液晶显示器组件的电源和接地轨道。
根据图4所示的测试设置,对LCD单元创建的电源和接地反弹进行了测试。
图4:用于测量电源(Vcc)和地面反弹[1]的测试设置
测试从Rev A版本的LCD PCBA开始。图6到图8所示的测量数据是由连接到图5所示低电感探头的泰克MDO4054C示波器捕获的
图5:用低电感探头测量地弹的方法
在3.3 V供电轨和输出线上发现了振铃,如下图(图6)所示。3.3 V供电轨上的振铃峰值值为524 mV。
图6。: CH1(黄色信号)3.3 V Vcc电源测量在LCD PCBA上STM32F4 IC的引脚91(电压偏移去除),CH2(蓝色信号)输出线引脚3 (LTDC_B0)
在地轨和输出线上也有振铃现象,如图7所示。地轨上的振铃峰值值为748 mV。
图。7: CH1(黄色信号)GND测量在LCD PCB组件上STM32F4 IC的引脚90,CH2(蓝色信号)输出线引脚3 (LTDC_B0) - TTL信号
后来发现,这个振铃被耦合到所有的数据线上,如下面的图8所示。
图8。: pin92 (CAN2_RX)带700mV振铃
这些瞬态电流产生的EMI噪声的谱含量超出了去耦电容器的能力。如果在这样的系统中加入去耦电容,系统将变成一个并行谐振电路,在边缘跃迁[3]期间产生振荡,使振铃变得更糟。由于设计不当的LCD驱动器PCB产生的电源和接地反弹造成了严重的EMI问题,因此必须研究适当的解决方案来缓解这些问题。
方案一:改变堆叠,增加平面电容
电磁干扰接收机的响应显示在高频区(100兆赫以上)有噪声。液晶显示器单元的控制器PCB设计为四层堆叠,其中一个内部平面为接地,一个内部平面为+3.3 V (VDD)。如图9所示,平面对被47+ mils的电介质分离。两架飞机都嵌入了信号轨迹,这影响了它们的完整性。我们希望减少高边缘率和糟糕的PCB布局在LCD显示器中造成的EMI问题的影响。
图9: LCD驱动PCB Rev A的层堆叠
在这种情况下,PCB中的平面电容可以通过在PCB级滤波噪声来减少EMI问题。根据[1],计算PCB中的平面电容,单位为法拉,如EQ(1)所示。
(1)
地点:
εo自由空间的介电常数是ε吗r是介电常数,A是PCB的面积,d是用于堆叠的介电厚度
LCD单元的原始PCBA在电源和地平面之间使用~47mils的介电。这不足以滤除任何高频EMI噪声。因此重新设计LCD PCB,在层堆叠中增加更多平面电容,如图10所示。3.3 V与地之间的介电厚度减少到3mil。由于驱动器PCBA中的一些逻辑电路也使用5v,因此在5v导轨上增加了另一个平面电容。动力和地面平面的设计也没有任何痕迹通过它们。对于设计中的所有集成电路,电源和接地网直接连接到各自的平面,确保尽可能低的线路阻抗。
图10: LCD驱动PCB Rev B的层堆叠
图11: 3米EMI测量-前水平- LCD显示Rev. A vs. Rev. B
PCBA新版本Rev B的EMI接收机响应与Rev A相比有显著改善(图11)。通过在PCB堆叠中添加平面电容,在200 MHz到1GHz范围内,可以降低~10 dB到~20 dB的EMI噪声,如图11所示。不幸的是,在实现PDN滤波器解决方案后,它将永远不可能减轻所有由LCD显示器地面反弹产生的EMI噪声。这是由于可用的微控制器包内返回路径固有电感的基本限制。这个问题与包装有关,很难通过在PCB上采取的措施来解决。接地引线中的电感并不是封装中唯一的电感;所有的输出引脚都有一个相关的电感。较好的解决办法是降低所有引线的电感。设计需要更新一个较低的寄生引线电感包,如球栅阵列(BGA)。
解决方案2:更换低电感微控制器封装
下一步是研究更多关于包和与每个包相关的典型寄生电感。各种IC封装的典型寄生引线电感如下表1所示。
表1:各种IC封装[5]的典型寄生电感
包 |
典型的寄生引线电感 |
包 |
典型的寄生引线电感 |
14针DIP |
3.2nH至10.2nH |
14脚SOIC |
2.6nH至3.6nH |
20针DIP |
3.4nH至13.7nH |
20引脚SOIC |
4.9nH至8.5nH |
40针DIP |
4.4nH至21.7nH |
||
40针TAB |
1.2nH至2.5nH |
208引脚QFP |
5.31nH至8.74nH |
44引脚QFP |
6.07nH至7.06nH |
100引脚QFP |
6.69nH至7.96nH |
20脚PLCC |
3.5nH至6.3nH |
119引脚PBGA |
0.15nH ~ 5.7nH |
28脚PLCC |
3.7nH至7.8nH |
249引脚PBGA |
0.13nH ~ 5.1nH |
44脚PLCC |
4.3nH至6.1nH |
624引脚CBGA |
0.5nH至4.75nH |
68脚PLCC |
5.3nH至8.9nH |
456引脚PBGA |
0.2nH ~ 5.8nH |
电感电压随时间的函数由式(2)给出。在这种情况下,边缘速率可以代替时间。
(2)
地点:
Vl=电压,单位为伏,穿过电感,L =电感值,单位为亨利,di =电流变化,单位为安培,dt =时间变化,单位为秒。
随着边率的增加(dt减小),Vl上升。随着模具收缩,di和边缘率(dt)都有助于V的增加l,这会在电源引线中造成较大的电压瞬变。
对于最大引线电感= 8.74 nH的208引脚QFP封装,假设di = 20 mA, dt = 2 ns,对于单个开关IO线开关(1位),从模具(包括线键合和引脚)穿过电感的电压如式(3)所示。
(3)
如果这个IC的10位同时改变Vl= 870 mV。
LCD驱动器PCBA中使用的STM32F4使用176引脚LQFP封装,每个引脚[2]的电感范围为7 nH到10 nH。如图7所示,在STM32F4单片机上测得的地跳值为~780 mV。STM32F4 datasheet指定di = 5 mA max每IO线。因此,从测量的地面反弹值可以计算出每个引脚的电感。理想情况下,如果计算的电感接近数据表指定的电感数,则目的是找到与测量的相关性。假设dt = 1ns,使用di = 5ma和Vl= 780 mV,故计算总电感为
(4)
因此,每个引脚的电感可以通过在捕获的780 mV测量期间除以24位有源来近似。
(5)
这与~ 7nh的176引脚LQFP封装与24位切换的RGB LCD接口相关。
不幸的是,LCD制造商还没有准备好改变IC封装。所以我们不得不转向其他可能的解决方案。
方案三:显示接口信号差
第三种选择是使用差分信号接口到显示器,作为并行RGB接口的替代方案。差动电路中的逻辑状态变化是相反的,因此从电源流出的电流保持稳定。这是差分信令相对于单端信令的一个更重要的优势。流过IC封装的电源引线的电流大小保持不变。因此,SSN的供应和地反弹在电源引线的电感上发展为零[1]。
机器人系统更新了一个新的液晶显示器,使用差分信号接口。液晶驱动器PCBA中使用了Renesas Synergy微控制器,具有176引脚LQFP封装(典型寄生电感~7nH至10nH)。图12所示的电磁干扰响应将新型液晶显示器与具有地弹跳的原始液晶显示器Rev A进行了比较。LCD Rev A与电源和地面反弹显示多个噪声峰值越过CISPR类B限制(如图12所示红线)。带有差分信号的新LCD显示器显示,只有少数噪声峰值超过了CISPR B类限制(图12中较低的红线)。与原来的液晶显示器Rev A版本相比,这显示了约20分贝的改进。使用更新的LCD显示,EMI发射峰值完全在CISPR A类限制范围内(图12上红线,右侧图像)。
图12: 3米EMI测量-前水平-液晶显示器Rev A(左)vs.带有差分信号的新型液晶显示器(右)
如图所示,差分信号是一个很好的解决方案,以减少电磁干扰产生的电源和地反弹。唯一的缺点是差分信号需要两根导线,两个连接器引脚,两个驱动器和两个接收器,这增加了额外的设计成本。
结论与总结
这些ic在设备级产生的EMI问题可以耦合到PCB,然后进入系统。这些EMI问题将导致产品延迟,并产生额外的合规性测试成本。由于IC封装的固有电感,涉及开关瞬态的频率太高,离散电容器无法支持。增加平面电容器来过滤高频噪声只能部分解决这类问题。如果设计的额外成本是可以接受的,差分信号是一个适当的解决方案,以减轻供应和地反弹。作为一种权衡,正是这些开关瞬态也可以迫使设计者使用寄生电感较低的BGA封装。
参考文献
Lee Ritchey, John Zasio, Kella Knack,第一次正确:高速PCB和系统设计的实用手册,超速边缘,2003年,第1卷。
[2] D3uzseaevmutz1.cloudfront.net。[网上]可于以下网址索取:https://d3uzseaevmutz1.cloudfront.net/pubs/misc/PackageGuide5.pdf
[3] Eric Bogatin,信号和功率完整性简化,Prentice Hall, 2010。
[4]关于地面弹跳及其测量方法。可以在:https://blog.teledynelecroy.com/2018/08/about-ground-bounce-and-how-to-measure.html
Michael Lamson,“封装在集成电路设计过程中占据中心舞台”《电子设计》,1998年6月8日。David Shear,《重新审视地面反弹试验》,EDN, 1993年4月。